Titan Coatings Available for All Your Vehicle Coating Needs
Elastomer VS Ceramic
Ceramic coatings have some disadvantages that make them unsuitable for various applications. The solid fractions of ceramics are composed mainly of quartz, making them relatively hard and stiff. This property makes ceramics brittle and susceptible to micro-cracking, making them unsuitable for applications that require flexibility. Additionally, ceramics have a low ability to absorb impacts, which makes them prone to breaking and cracking when subjected to stress. Moreover, ceramics lack the self-healing capability of elastomers, and when they experience stress, they tend to crack and propagate until the material fails.
In contrast, elastomers are much better than ceramics due to their unique properties. Elastomers have a high capacity for self-healing and can recover their original shape after reaching their softening point. This property makes them highly resistant to wear and tear, making them ideal for applications that require durability. Furthermore, elastomers are inherently flexible, which makes them highly suitable for applications that require materials to bend and stretch without breaking. Elastomers have a much greater thickness compared to ceramics and can withstand a wide range of temperatures without cracking or breaking.
If you look at this phenomenon at the microscopic level, it turns out that approximately a quarter-micron layer of quartz bends along with the clear coat layer at the furthest, and it is the paint itself that shows little flexibility/self-leveling. In the case of elastomer, with similar material consumption, we have 1 to 2 microns (correct - micrometers) and much greater thickness and, above all, a real self-healing capacity.
In conclusion, ceramic coatings have several disadvantages that make them unsuitable for various applications. Elastomers are much better than ceramics because they are highly flexible and have a high capacity for self-healing. Elastomers are durable and highly resistant to wear and tear making them ideal for a wide range of applications. It is essential to understand the unique properties of these materials to choose the right option for a particular application. Therefore, when it comes to choosing between ceramics and elastomers, elastomers are the clear winner.
Stop by for your free assestment in regards to product application and configuration.
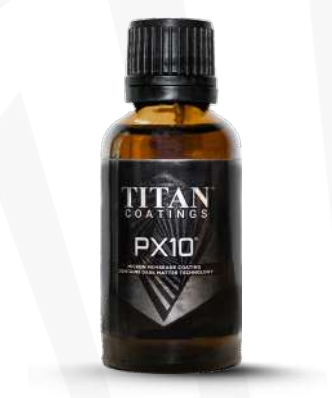
PX10
Parameters
Coating type: base coat
Durability: up to 6 years
Contact angle: 105 degrees
Thickness: max 12 microns
Thermal resistance: -40 ° C + 600 ° C
Chemical resistance: 1-14 pH
Self-healing ability: none
Expenditure: 15-20 ml per layer
Benefits
- Super Underlay
- Self-Cleaning and Oleophobic
- Deep Shine and Resistance Against UV / UVB
- Special Resistance Against Chemicals
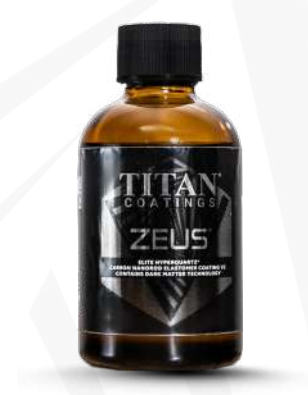
Zeus
Parameters
Coating type: base or standalone coating
Durability: up to 10 years in two layers
Contact angle: 120 degrees
Thickness: max 5 microns
Thermal resistance: 600 ° C
Chemical resistance: 1-13 pH
Self-healing ability: regular
Expenditure: 15-20 ml per layer
Benefits
- Limited Adhesion of Insects
- Self-Cleaning and Oleophobic
- Special Resistance Against Chemicals
- Deep Shine and Resistance Against UV /UVB
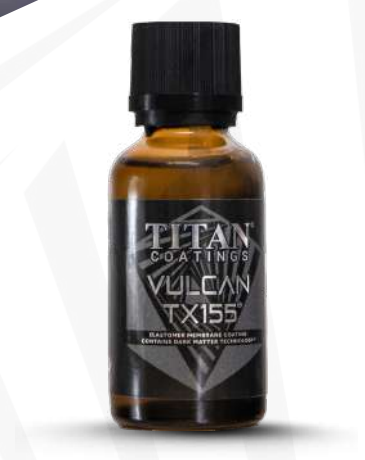
Vulcan
Parameters
Coating type: stand alone coat or top coat
Durability: up to 6 years
Contact angle: 115 degrees
Thickness: max 5 microns
Thermal resistance: 600 ° C
Chemical resistance: 1-13 pH
Self-healing ability: strong
Expenditure: 10-20ml per layer
Benefits
- Limited Adhesion of Insets
- Self-Cleaning and Oleophobic
- Capacity for Regeneration
- Special Resistance Against Chemicals
- Deep Shine and Resistance Against UV /UVB
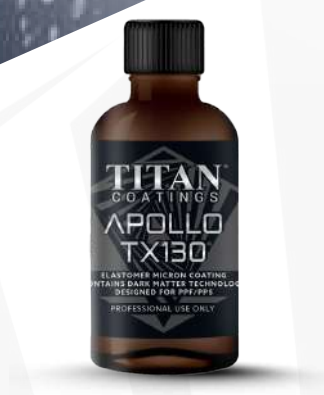
Apollo
Parameters
Coating type: stand alone coat
Durability: up to 5 years
Thermal resistance: 600°C
Chemical resistance: 1-14 pH
Self-healing ability: strong
Expenditure: 5-15ml per layer
Benefits
- Limited Adhesion of Insets
- Self-Cleaning and Oleophobic
- Capacity for Regeneration
- Special Resistance Against Chemicals
- Deep Shine and Resistance Against UV /UVB
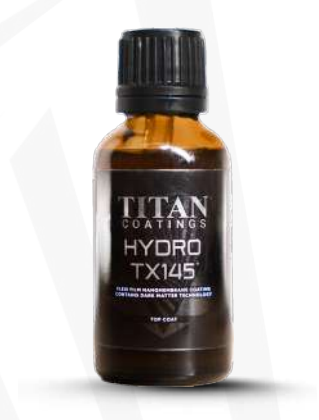
Hydro
Parameters
Coating type: top coat
Durability: up to 3 years
Contact angle: 105 degrees
Thickness: max 100 nm
Thermal resistance: -40 ° C + 600 ° C
Chemical resistance: 1-14 pH
Self-healing ability: none
Expenditure: 10-15ml for layer
Benefits
- Limited Adhesion of Insets
- Self-Cleaning and Oleophobic
- Extremely Slippery Varnish
- Special Resistance Against Chemicals
- Deep Shine and Resistance Against UV /UVB
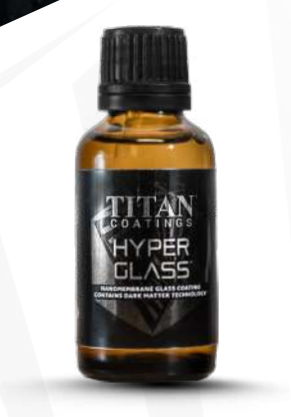
Hyperglass
Parameters
Durability: up to 5 year or 25k
km in two layers
Contact angle: 110 degrees
Thickness: max 100nm
Thermal resistance: 600 ° C
Chemical resistance: 1-13 pH
Expenditure: 5-8 ml for two layers
Benefits
- Limited Adhesion of Insets
- Self-Cleaning and Oleophobic
- Special Resistance Against Chemicals
- Water Discharge from 50 KM/H
- Security While Driving in the Rain
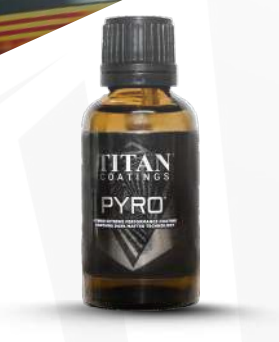
Pyro
Parameters
Durability: up to 10 years
Contact angle: 105 degrees
Thickness: max 4 micron
Self-healing ability: 1500 ° C
Chemical resistance: 1-13 pH
Benefits
- Exceptional Thermal Resistance
- Special Resistance Against Chemicals
- Limited Dust Adhesion From Brake Pads
- Self-Cleaning and Oleophobic
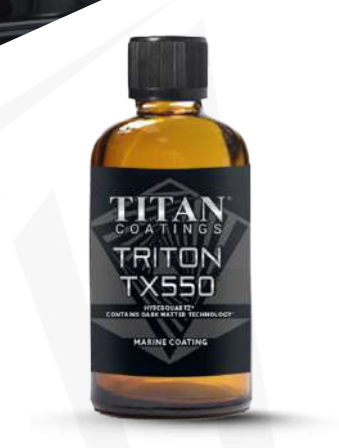
Triton
Parameters
Coating type: base and top in one
Durability: 3 years below the waterline, 5 years
above the waterline
Layering / «sandwiches»: with Hydro TX 145
Thickness: max 5 microns
Stiffness: 9H
Thermal resistance: 600 ° C
Chemical resistance: 1-13 pH
Benefits
- Limited Sticking of Lichens
- Self-Cleaning and Oleophobic
- Special Resistance Against Chemicals
- Smaller Water Resistance
We’d love to hear from you! Call our friendly team at 808-366-8360.